Automated foam concrete production line AMK "StroyFoamBeton 80 SR" (with included cutting plant URK MASTER PLUS LOGIC)
1 - Bag unloader SR 500 (1000) with screw conveyor of VK series (6 m by length) (cement conveying); 2 - Belt conveyor LK 500 (7 m by length); 3 - Feed bin for inert materials RB 3000; 4 - Batching hopper of inert and biding components with knife gate; 5 - Mixing complex RBS 1000 HYACINTH with disk gate and pneumatic drive; 6 - Automated control system SAU 600 LOGIC; 7 - Control board of air-operated system of the line; 8 - Liquid compoennets baching and preparation plant SJK 4000; 9 - Universal cutting plant URK MASTER PLUS LOGIC; 10 - Metal moulds FORMBLOCK-MASSIVE; 11 - Air compressor K2; 12 - Peristaltic (hose) pump KORNET 7; 13 - Bin of peristaltic pump KORNET 7 (0.5 m³); 14 - Control board of peristaltic pump KORNET 7.
In order to satisfy the constantly increased demand for foam concrete products more and more attention is paid to problems of development of modern mini-plants to produce such construction material. The industrial equipment is always improved, the automatics degree of all production processes is increased. Al these actions are made for only one purpose to get qualitative products met fully the modern demands.
The engineering enterprise "Stroymechanika" going with the times, designs and supplies the reliable and highly profitable equipment to produce foam concrete. The equipment produced by our enterprise is a turnkey production line allowing to make foam concrete mortars and mould high qualitative geometrically exact foam blocks.
The automation of engineering processes of foam concrete articles production allows not only to reduce the prime price of final products, but increase considerably the stable character of its main features minimizing the influence of human factor especially at components batching. The automated system SAU 600 LOGIC is included in the AMK to solve the question of process automation.
The system SAU 600 LOGIC adjust the operation of:
- Bulk bags unloader SR 500 (1000) with screw conveyor of "VK " series (6 meters by length) (cement conveyance);
- Belt conveyor LK 500 (7 meters by length) (sand conveyance);
- Weighting bin of inert and binding materials (weigh batching of inert and binding materials entering the mixing plant);
- Slide gate "Butterfly " with air-operated drive (loading of mix basic components into mixing plant);
- Liquid components preparation and batching plant SJK 4000 (batching supply of water and liquid components to the mix);
- Mixing plant "HYACINTH" (foam concrete mix making);
- Sphincter valve of ready mix unloading from mixing plant (unloading of ready mix).
The approximate layout of the line AMK "StroyFoamBeton 80 SR" on the production site:
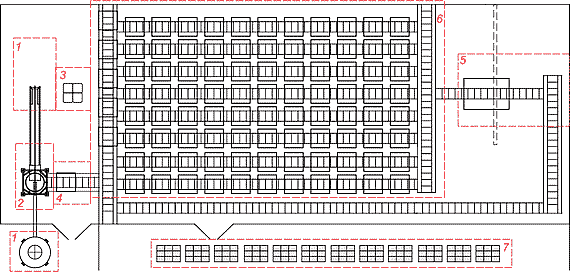
1. Raw material storage.
The bulk bag unloader SR 500 (1000) with screw conveyor of series "VK" (6 meter by length) is used to supply cement. The sand is delivered by tip lorries. The sand is loaded to feed bin for inert materials by help of front wheel loader that is installed under belt conveyor of "LK" series or its analogue.
2. Liquid components preparation area.
Water is poured into plastic tanks of the preparation and batching plant SJK through pipelines in order. The concentrate and all required water is poured into the foaming agent tank, the required water and additives are poured into chemical agents tank. The liquid components (foaming agents and chemical additives solutions) are mixed by recycling pumps built in sidewall of the tank, are heated by heating elements.
3. Mixing area.
The mixing section includes: metering bin of inert and binding materials on the frame, mixing plant with embedded foam generator TRITON 5M, compressor. The water and liquid components are batched in given order in concrete mixer. The cement enters the metering bin by screw conveyor of "VK" series, then enters the mixing plant in accordance with rate of application for correspondent concrete density. The sand enters the metering bin and then mixing plant from feed hopper of inert materials with help of belt conveyor. After that all components has been loaded, the mortar is mixed to homogeneous mass, then the technical foam of given ratio multiplicity factor enters the mixing plant RBS HYACINTH by help of foam generator where the mix is mixed for ready mass.
4. Moulding area.
The ready foam concrete mix is evenly pumped into moulds FORM MASSIVE through drain valve of the mixer RBS 1000 HYACINTH by excessive pressure. A mould consists of two parts - a technological pallet and removable interchangeable borders. The technological pallet is four-wheel trolley with metal foundation. Before to pour the foam concrete mix the removable borders are greased and installed on the pallet.
5. Foam concrete sawing area.
As the foam concrete is hardened, the locks of borders of the FORMBLOCK MASSIVE are opened, the massive is removed from foundation and moulded foam concrete massive is entered the working area of the cutting plant URK MASTER PLUS LOGIC on the technological pallet. The massive is passed through screw knife of the cutting plant, then it is supplied under carriage of the cross cutting then under the carriage of length cutting. The carriages are lifted and with help of electric-powered drive, and string travel with help of gear motor. After the cutting cycle is made, the foam concrete articles are removed from the mould pallet and are transported to dry up.
6. Heat processing area.
Using the tracked locomotion techniques in the production shop the heat processing section is equipped with technological tunnels where the hot air is boosted by convector heaters or the "heat-insulated floor" are built in the foundation, as well as the installation of heating radiator is possible. The chamber use allows to accelerate the setting process as well as to get foam concrete with increased strength characteristics.
7. Foam concrete finished-products storage area.
After thermal processing the finished blocks are palletized, and wrapped with film. The pallets with foam concrete blocks are kept in finished-products storage area before 70% hardening. The temperature should be no less than +15°С. The pallets with blocks are installed in three tiers, the minimal capacity is estimated on the base of everyday capacity.
The competitive advantages of the AMK "StroyFoamBeton 80 SR":
- Operation in manual and automatic mode due to high automation level;
- Application of spare parts of well-known world manufacturers: components for air-operated system
(FESTO, Germany), gear motors of (MOTOVARIO, Italy), control chamber components (LG, South Korea), (ABB, Germany), logical controllers of (ABC-MK, Russia);
- High batching accuracy of used materials: 0,1%-0,2% allows to reduce the prime price;
- The geometrical accuracy and well-designed general view of ready products will satisfy the most exacting customer;
- High capacity ensures the productive efficiency.
Content of the line AMK "StroyFoamBeton 80 SR" capacity 80 m³/shift:
№ |
Designation |
Technical characteristics |
Quantity |
1 |
Bag unloader SR-1000 with screw conveyor of "VK" series (3,5 meters by length) (cement conveyance) |
Overall dimensions 2500×1540×1540 mm Weight 385 kg |
1 set |
2 |
Belt conveyor LK 500 with loading bin (7,4 meters) (sand conveyance) |
Overall dimensions 8000×1020×595 mm Power consumption 5 kW Capacity 10 t/h |
1 set |
3 |
Metering bin of inert and binding materials with knife gate |
Overall dimensions 2060×2060×3117 mm Air-operated drive of the knife gate of FESTO production |
1 set |
4 |
Mixing complex RBS 1000 HYACINTH with slide gate and pneumatic valve |
Overall dimensions 1750×1200×1850 mm Power consumption 11 kW Capacity up to 10 m³/h |
1 set |
5 |
Automatic control system SAU 600 LOGIC |
LG element base Overall dimensions 600×360×600 mm |
1 set |
6 |
Control box |
FESTO Air operated drive (Germany) Overall dimensions 600×500×200 mm |
1 set |
7 |
The liquid components preparation and batching plant SJK 4000 |
Overall dimensions 2500×2100×1165 mm Напряжение питания 380 В |
1 set |
8 |
Universal cutting plant URK MASTER PLUS LOGIC |
Overall dimensions 3600×2400×2700 mm |
1 set |
9 |
Metal mould FORMBLOCK-MASSIVE |
Overall dimensions 1450×1450×750 mm |
1 set |
10 |
Air compressor К 2 |
Overall dimensions 130×62×125 mm Потребляемая мощность 5,5 кВт |
1 set |
11 |
Peristaltic (hose) pump KORNET 7 |
Overall dimensions 1190×850×641 mm Weight 170 kg |
1 set |
12 |
Peristaltic pump KORNET 7 bin (0,5 m³) |
Overall dimensions 1300×1100×1100 mm Weight 250 kg |
1 set |
13 |
Control box of peristaltic pump KORNET 7 |
Overall dimensions 395×310×220 mm |
1 set |
14 |
Cables |
|
1 set |
15 |
Hose of air-operated system |
|
1 set |
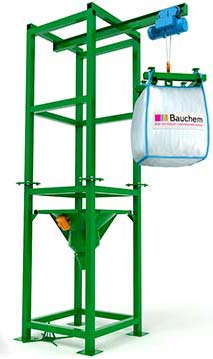 |
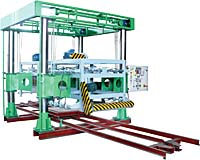 |
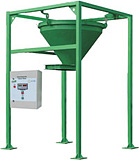 |
Bulk bag unloader SR 1000 |
Universal cutting plant URK MASTER PLUS LOGIC |
Metering bin of inert and binding materials with knife gate |
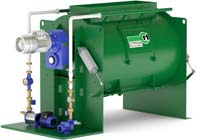 |
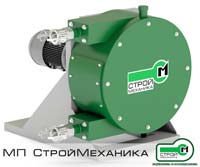 |
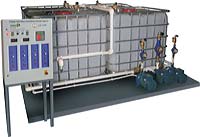 |
Mixing plant RBS HYACINTH |
Peristaltic (hose) pump KORNET 7 |
Liquid components preparation and batching plant SJK 4000 |
The line "StroyFoamBeton" enters the customer run and tested.
The delivery set of the line includes:
- Operating manual;
- Service manual for SAU 600 LOGIC;
- Engineering schedule for production of articles on the line AMK "StroyFoamBeton".
|