Universal cutting plant (URK) MASTER PLUS (LOGIC) (cutting of cellular concrete masses)
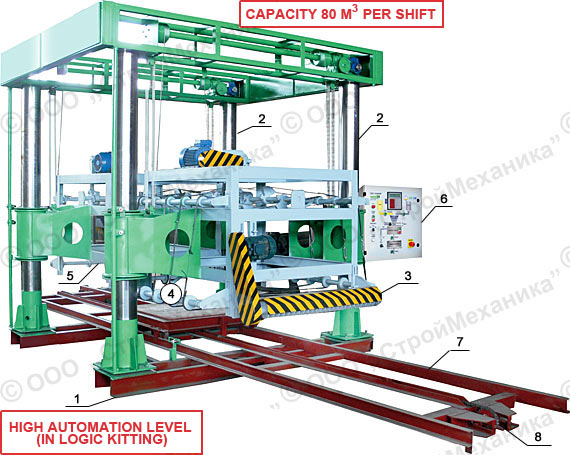 1 - Montage foundation frame; 2 - Guiding supports of carriages of cross and length cutting; 3 - Screw knife unit; 4 - Carriage of cross cutting of the massive; 5 - Carriage of length cutting of eth massive; 6 - Automatic control box SAU URK LOGIC; 7 - Transportation rails; 8 - The system of molds transportation with electro mechanic drive (in LOGIC kitting).
The universal cutting plant (URK) MASTER PLUS by the production of the engineering enterprise "Stroymechanika" is intended to make wall and partition cellular concretes (foam concrete, gas concrete) with geometrical deviations from given dimensions but no more than ±2 from the mass with overall dimensions up to 1200×1200×600 mm in the shops. The reached cutting accuracy helps to lay blocks on glue or thin-layer mortars.
The design of carriages of cutting complex allows to get blocks with different dimenss with application on one set of portable metal moulds. The cutting of foam concretes is carried out with help of special steel strings (saws) manufactured separately with use of the winding plant STRING 500. The cutting complex (Sawing complex) (URK) MASTER PLUS can be equipped as with strings as with saws according to customer's desire.
In order to cut the homogeneous blown (porous) cellular concrete (foam concrete, gas concrete) made in full conformity with GOST 25485-89 is used. The material rather hardened to be cut (4-12 hours after pouring into mould) is slit on the cutting complex MASTER PLUS.
Operation on the cutting complex.
The light-weight concrete mix enters the portable metal moulds FORMBLOCK-MASSIVE specially developed to be used as a part of cutting system. The portable metal mold FORMBLOCK-MASSIVE used as a part of cutting complex is easy in operation. It takes 2-3 minutes to clean, grease, and assemble one metal mould.
The cellular (foam) concrete hardens (4-12 hours depending on the characteristics and mixing technology) at temperature 20-35 °С. The crossbeam designed for operation with portable metal moulds FORMBLOCK-MASSIVE is used to supply metal moulds to the working section of the cutting complex as well as for transportation to the maturing section. After the foam concrete have been hardened, the boards locks of the moulds are opened, the moulds are removed from the foundation, the molded foam concrete enters the working section of the cutting complex on the technological pallets. The foam concrete masses is conveyed through screw knife of the upper layer cutting, then the mass is supplied under the carriage of the length cutting, then through the carriage of the cross cutting of the mass. The lifting and drop of the carriages with strings (saws) is made electromechanically, and the step of the string (saws) is made by gear motor. After the cutting (processing) has been made, the foam concrete articles are removed from the pallet of the mould and transported to the section to be dried. The transportation of the ready articles from the cutting area is made by the gripping device for mould handling, the design of the gripping device provides the possibility to adjust the stack of removing products under the specified dimension, as well as the slip of the ready products is excluded.
If the transport system with railway lines is applied on the production site, the section area is equipped with technological tunnels in which the warm air is boosted by heat guns to finish drying, or the "warm floors" are built in the foundation, the installation of the heating system radiator is possible. After the articles are matured, they are stacked on the wooden pallets, packaged with film and transported to the finished-products storage area.
Consult with our managers if the dimensions and strength of foam concrete mass differ from the specified ones.
The automatic control system of the cutting unit.
The application of automatic control system SAU URK LOGIC the unit can be controlled as manually as automatically. The automatic control system of the cutting plant SAU URK LOGIC includes a control box with control board installed on it, cables, and set of sensors, required for automatic operation of the complex. The cutting plant is controlled in automatic mode by pressing the button "START" on the front panel of the control box and the massive in automatic mode is cut into blocks of specified dimensions.
The drive of the screw knife and the drive of string mechanism have the variable frequency drives helped to adjust the oscillation frequency of the strings and rotational speed of the screw knife in order to choose more qualitative surface of the processed mass. There is also the possibility to adjust the displacement speed of cutting carriages that helps to set up the necessary processing frequency of the block surface (from smooth to deep wave).
The automatic control system SAU URK LOGIC keeps track of the operation of:
- The transporting mechanism of metal molds transportation to the cutting area (supply and installation of the technological pallet of the mould with foam concrete mass);
- The screw knife (cutting of upper layer of the mass);
- The carriage of cross cutting (cross cutting of the foam concrete);
- The carriage of the length cutting (length of the foam concrete mass).
In order to provide the safe operation of the cutting complex the complementary inductive probes installed on the end points are used.
The application of automatic control system SAU URK LOGIC (CAM system) allows to reduce the staff worked on the production site that has a good influence on payback speed of the complex and quality of the launched products.
Table 1: Dimensions of article received on the cutting complex
Dimensions |
Quantity |
600×300×200 |
24 |
600×300×100 |
48 |
600×400×300 |
12 |
600×400×200 |
18 |
600×400×100 |
36 |
The delivery of the articles with other dimensions is possible.
The operations, carried out on the cutting complex URK MASTER PLUS:
- Transportation of the technological pallet with foam concrete mass to the operating area of the cutting complex;
- Transportation of the technological pallet with foam concrete mass under screw knife to remove upper layer;
- Supply, positioning and fixation of the technological pallet under the carriage of cross cutting of the foam concrete mass;
- Supply, positioning and fixation of the technological pallet under the carriage of length cutting of the foam concrete mass;
- Displacing of the technological pallet with articles from the cutting area.
Table 2: Composition of the cutting complex URK MASTER PLUS
Nomination |
Quantity |
Montage foundation frame |
1 |
Unit of upper layer removal of the foam concrete mass |
1 |
Carriage of mass cross cutting |
1 |
Carriage of mass length cutting |
1 |
Automatic control system chamber SAU LOGIC |
1 |
Automation block of supply and positioning of the metal mould |
1 |
Hydraulic station |
1 |
Hydraulic mechanism of the metal mould supply |
1 |
Transport route |
1 |
Portable metal mould FORMBLOCK MASSIVE |
1 |
Table 3: The complementary equipment of the cutting plant URK MASTER PLUS
Competitive advantages of the cutting complex URK MASTER PLUS:
- The high automation degree of the cutting complex, as well as the operation as in automatic as in manual regime are possible with application of the automatic control system SAU URK LOGIC.
- Low power consumption became possible with the application of power-intensive high-torque drives.
- High capacity of the complex will provide the productive efficiency.
- The quick payback is possible thanks to not high price.
- The short period of putting into operation allows to start the production and seeling of the products as quick as possible.
The geometrical accuracy and good appearance of the made products will satisfy the hard-to-please client.
- The application of the carriages as a hydraulic drives helps to minimize the power inputs.
- It is possible to produce the integrated complexes (strings, saws).
- The operation as in automatic as in manual regime due to high automation level.
- The application of qualitative and reliable components of well-known world manufacturers:
components of the hydraulic system of (ATOS, Italy), (MP FILTRI, Italy), logic controllers of (АВС-МК, Russia), gear motors of (CHIARAVALLI TRANSMISSIONI, Italy).
Applying the cutting complex URK MASTER PLUS on the production site the opportunity to enlarge the range of launched products has arose, as the application of one mould FOMRBLOCK MASSIVE helps to make blocks of 5 standard dimension types. Besides, the moulds FORMBLOCK MASSIEV are cheaper in some times than the cassette moulds, and the production of such moulds does not require complex equipment, that's why the customer can make them by himself.
Technical characteristics
Capacity, m³/h |
12 |
Rated power , kW |
12 |
Overall dimensions (L×W×H), mm |
9000×2500×2700 |
Weight, t |
2,2 |
Requirements to the installation place: - length of the area (without servicing area), m - width of the area (without servicing area), m - height of the area - ambient temperature, °C |
12 3,1 3,1 >5 |
Quantity of simultaneous cut masses, ps |
2 |
Maximum dimension of sawed mass (L×W×H), mm |
1200×1200×600 |
Cutting cycle of one mass, min |
5-7 |
Dimensions of ready blocks, mm |
table 1 |
Quantity of workers, persons |
1-2 |
Operating regimes |
Automatic/manual |
Ordering the cutting complex URK MASTER PLUS the drawings on moulds are offered free of charge, the cutting complex includes one mould FORMBLOCK-MASSIVE that can be served as a sample for the independent manufacturing of required quantity of moulds.
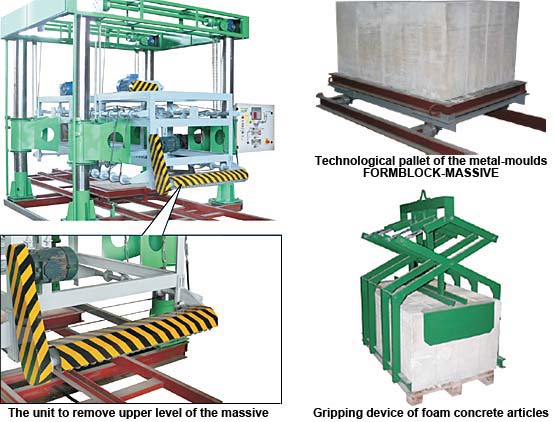
Complementary services:
The application of the cutting plant URK MASTER PLUS reduces a lot the costs and increases the efficiency of your business.
|